Case Study: Alexandria Industries
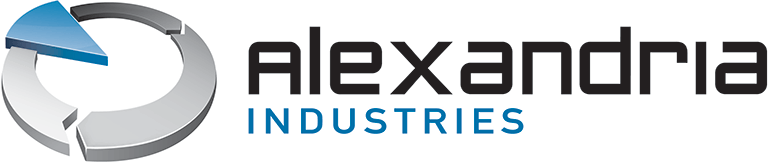
Alexandria Industries, with ISO 9001:2015 certified facilities, delivers customized aluminum extrusions with precision machined features, as well as plastic injection molding, finishing, welding and assembly services. Alexandria Industries (A.I.) is headquartered in Alexandria, MN, with manufacturing locations in Minnesota, Indiana and Texas.
In addition to regular calibration of all measurement systems and equipment, in 1999 A.I. began a new program for machine tool calibration. The performance of their CNC machine tools were regularly checked for linear accuracy with a laser interferometer and volumetric performance with a telescoping ball bar.
Every CNC calibration performed by A.I. provided a detailed analysis of linear and volumetric performance as well as the opportunity to optimize performance through software and mechanical compensation.
The goal of the machine tool calibration program was to improve process and production volume by gaining a better understanding of the value-added machining process offered to their customers. The second goal was to reduce material costs by reducing scrap. The calibration program also supports the company’s commitment to quality manufacturing and a demand to expand its customer base.
Both production and scheduling personnel can now review calibration data and determine what machines are best suited to a given work order based on its manufacturing requirements. By reviewing the tolerance requirements and the machine data they can schedule a project to the right area knowing that it can be manufactured to customer’s requirements.
A byproduct of the calibration process helped the company with machine tool evaluation and purchasing additional machines based on historical calibration data. Reviewing historical machine performance, allowed A.I. to purchase machines with a lower entry cost, service them on a scheduled basis and track their performance.
Implementing the calibration program, afforded A.I. the knowledge and process insight to substantially grow their customer base into new areas of manufacturing, including medical, automotive and aerospace components. The company delivers complex components that go into their customers’ products.
Scrap has decreased over the program’s life. It has helped with improved performance and fewer machine incidents. PQI also streamlined all documents and purchasing requirement- related events to minimize administrative resources. All work is tracked and managed by PQI under a single blanket PO thereby reducing A.I. administrative time.
PQI tracks each machine, its calibration cycle and service due date. Our service coordinators know over a four-year period what machines need service. Our technicians and standards are scheduled accordingly. A once yearly phone review adjusts the agreement by adding new pieces of equipment and removing items that have been retired.
A program of preventive maintenance is well accepted and widely implemented in countless manufacturing organizations. The best organizations take this a step further and use the tools of predictive maintenance to understand and act on potential problems before they occur. Alexandria Industries and Productivity Quality, Inc. have collaborated on a successful program of preventive maintenance for 22 years.
If you would like to learn more about how this could be applied in your organization please contact us.